Mining & Process Solutions has won the top prize at this year’s Innovator of the Year awards, with an environmentally friendly, cost-efficient new process for the mining industry.
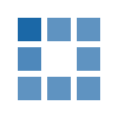
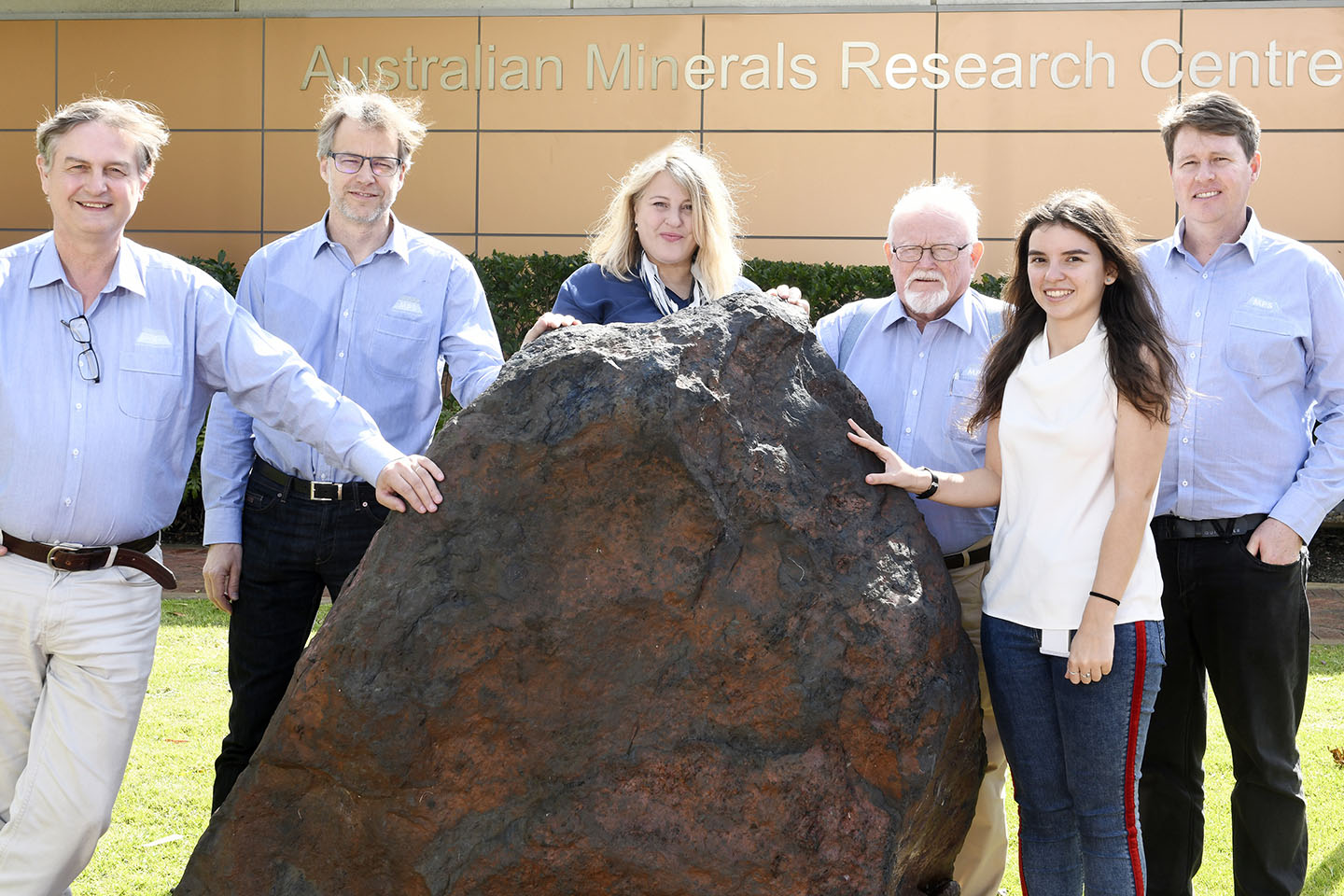
Mining & Process Solutions has won top prize at this year’s Innovator of the Year awards, with an environmentally friendly, cost-efficient new process for the mining industry.
Ivor Bryan came to this year’s Innovator of the Year judging panel with a taste for the theatrical.
Having pioneered GlyLeach, a process that uses the amino acid glycine to leach precious and base metals, the managing director of Mining & Process Solutions chose to display the liquid’s non-toxic credentials by drinking a glass of the substance (watered down) in front of the judges.
“It’s just a bit of theatre, right,” the 35-year mining industry veteran told Business News of his stunt.
With leaching generally associated with potentially toxic deposits and ore by-products, Mr Bryan wanted to illustrate a rethink of leaching that put environmental concerns top-of-mind.
“That’s why I’m so passionate about this,” Mr Bryan told Business News.
“It’s a fantastic alternative to acid and cyanide and the world needs it, quite frankly.”
It was the development and commercialisation of a non-toxic, low-cost leaching alternative that won MPS the top prize at this year’s state government-run Innovator of the Year awards, sponsored by Rio Tinto.
When Mr Bryan founded MPS with technical director Frank Trask and process consultant Tim Newton in 2014, he had already experimented with how to extract valuable metals from waste materials.
Working out of CSIRO’S Minerals Research Centre, Mr Bryan described being fascinated with Curtin University’s research into glycine leaching in 2016.
“The unique thing Curtin University discovered was that, when you put metals into an alkaline, it’s very selective in how it leaches base metals, like copper, nickel, cobalt and zinc, and precious metals like gold, platinum and silver,” he said.
“It doesn’t take some of the less-valuable metals that cause problems, like iron and magnesium, into the solution.
“When they get in, it’s kind of a nightmare because they’re not as valuable, so this is a big step forward over the alternatives.”
Mr Bryan said leaching generally required the use of sulphuric acid or cyanide, which while cheap and abundant, came with large amounts of waste and carried associated disposal costs.
The industry had tried to move away from the two chemicals for years, he added, as the waste, which was stored in tailings dams, contained large amounts of cyanide and acid that oxidised and caused acid mine drainage.
“We put all these things in behind a dam, and in many cases it’s got a legacy of hundreds of years where it’s chemically doing things,” Mr Bryan said.
Glycine, on the other hand, is broken down almost immediately after use.
“At neutral pH, bacteria will eat it and it degrades,” Mr Bryan said.
“It degrades to ammonia, so it’s harmless.”
Since buying the rights to the technology and patenting it as GlyLeach, MPS has hired 15 staff members and begun sourcing waste slag and ore for testing the process.
The business is now working with key players in the industry, including Newcrest Mining on the gold-copper Telfer mine, which is nearing end-of-life.
Mr Bryan said Newcrest Mining became interested in GlyLeach because the Telfer mine contained low-grade gold ore with elevated copper, which standard cyanide leaching could not effectively separate.
If that trial proves successful, the new process could translate to hundreds of millions in savings per annum for the company, as well as additional years in mine-life.
Elsewhere in Australia, Evolution Mining was trialling GlyLeach at its Cowal project in NSW, where a tailings dam nearby has caused unease for the community.
“We’ve done a first round of piloting and we’re about to start the second round, and we can actually eliminate cyanide waste in the tailings and save money by reducing cyanide,” Mr Bryan said.
He said he hoped the Cowal project would commercialise rapidly, with Telfer likely to take longer as it went through feasibility assessments.
The process has been well received by the mining industry, with MPS having undertaken test work for unspecified mid-size and large mining companies, Mr Bryan said, although the company had achieved most success with small explorers.
“We tackle all levels of mining companies, because some of those [smaller companies] see that some of these untreatable deposits are treatable, and we should be out there looking for them,” he said.
That’s led to trial work with mining companies in Zimbabwe, Tanzania and Chile.
Mr Bryan said these groups were trialling its use in the leaching of a tailings dam filled with gold ore with elevated copper, with early success in extracting saleable gold and copper leading him to believe MPS can scale-up operations in those countries.
Elsewhere, the company has employed agents in the US, Canada, Chile and South Africa to license the technology, with existing partnerships in Zimbabwe and Tanzania helping validate the case for GlyLeach’s effectiveness.
Domestically, Mr Bryan said the focus would remain on demonstrating the process’s success in smaller companies to make the case for viability with mid-size and larger companies.
“The first thing we’re asked [by larger businesses] is, where is this happening and where are you doing this?” he said.
“We’ve set up the commercial arrangements to encourage early adopters, so once we can demonstrate this in different jurisdictions and applications, it’ll sell itself.”
The goal then will be to transform from a service-based company that relies on trial work and grants towards one focused on IP management, licensing and research investment with income generated through royalties.
In the long term, Mr Bryan described an ambitious mission to fundamentally change how leaching was executed globally.
“Right now, for every material we pull out of a mine, around 3 per cent is valuable,” he said.
“The process of bringing the material from the mine to the processing plant and putting it through energy intensive mills represents around 80 per cent of costs and energy in the mining process.
“Why not just leave it in the ground, leach what we need from it with a non-toxic chemical, pump the material to the surface and extract the metal?”
With that in mind, Mr Bryan sad GlyLeach could one day make the energy intensive mining process nearly invisible, eliminating the need for tailings dams or any surface footprint.
“I think that’s attainable, but ambitious,” he said.